You will find that almost every industry around you is working via supervisory control and data acquisition (SCADA) system. This is the kind of system upon which the whole industrial work depends a lot. We can also say, SCADA is an automation control system which gives an insight to the supervisors about the plant conditions. It is used in almost all industrial verticals to access the entire plant from a control room. Let’s understand more about SCADA and its existence in previous years.
Before SCADA, industrial revolution took a drastic turn as industry 3.0, which started through partial automation, where industrialists used memory-programmable controls and computers. During this revolution, the internet was introduced as the major breakthrough for everything around us. The invention of computers and software was termed revolutionary and led to task automation, which was also known to be intelligent automation.
Talking about SCADA system, it is the supervisory control and data acquisition system of software and hardware that enables the industries to control processing from both local and remote locations. Many industries like water, wastewater systems, power, oil and gas, manufacturing, and food production use SCADA systems to collect, monitor, and process the real-time data. Furthermore, with the introduction of SCADA it was made a lot simpler to manage the industrial processes and have a direct interaction with devices like valves, pumps, & motors. The SCADA helped the industries to monitor and control industrial equipment in every segment like development, manufacturing, production, and fabrication. A basic SCADA system comprises of:
⦁ Human machine interface
⦁ Supervisory system
⦁ Remote terminal units
⦁ Programmable logic controllers (PLCs)
⦁ Communication infrastructure
⦁ SCADA programming
All these components when combined, form a functionable SCADA system where human machine interface is an input-output device, allowing a human operator to control the data. Supervisory system is a communication server that connects the human machine interface with other equipment like PLC and sensor devices. The remote terminal units are used for transmitting the recorded data to the supervisory systems. Additionally, PLCs- Programmable Logic Controllers work through sensors and contribute a major part in providing real-time monitoring of industrial processing.
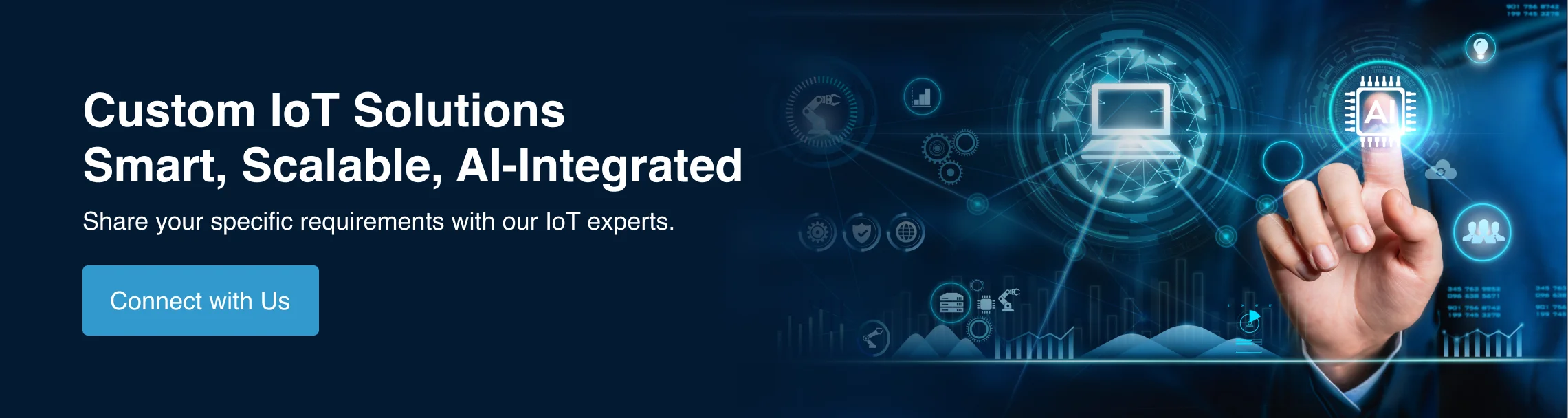
How a SCADA system works? :
1. Data Acquisitions:

The SCADA systems are important and reliable because they give a large chunk of data to make intelligent business decisions. Sensors, controllers, and real-time units play a major role in collecting data. The real-time system consists of a large number of sensors which collect the real-time data. And to ensure that the whole system works perfectly, it is important to monitor these sensors.
2. Data Communication:

The SCADA system uses wired network to effectively communicate between the user and devices. This enhances the efficiency of the sensor devices and lots of data is fetched via sensors and this data must be kept secured for effective data communication. SCADA systems thus use network communication for data transmission.
3. Data Presentation:

As a large amount of data is collected through sensor devices, converting this data into useful information becomes the most important task. As it becomes complex to handle large no. of sensors simultaneously, SCADA system uses Human-Machine Interface (HMI) to gather all the data from sensors and turn it into effective information.
4. The Human-Machine Interface:
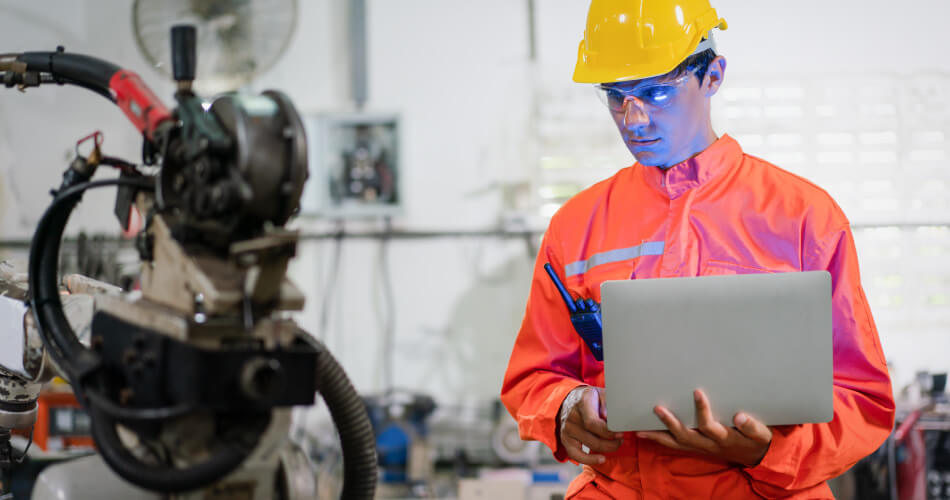
As SCADA uses HMI, the information displayed needs to be monitored by humans. It provides the access of multiple control units and PLCs.
5. Controlling and Monitoring:
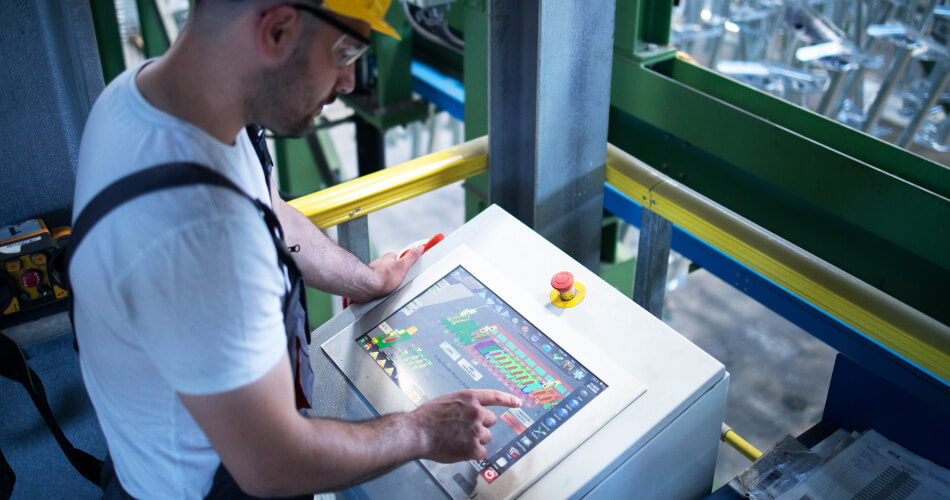
SCADA systems use switches to operate each device. These switches help in turning ON/OFF each device. SCADA systems work automatically without human intervention but in certain situations, it is to be handled by manually.
Talking about technology, the future of industrial automation is evolving in such a way that robots are replacing people. And now is the time for a greater revolution with the introduction of Industrial Internet of Things or Industry 4.0.
The Internet of Things is an advanced concept that industries are now widely accepting due to sensor-based techniques and data-driven approach. It enables the industrialists to strategize their business decisions and improve upon the loopholes to serve with better quality. For instance, if a SCADA system is generating detailed reports, using an IoT solution can improve the format and provide them in a much simpler and effective way. Moreover, the technology solutions assist in sharing the reports directly to the headquarters or any specific person. Now, let’s understand how IoT took over PLCs and SCADA system.
It is predicted that trillions of devices will be connected to internet in the coming years. Industry 4.0 is an era and a revolution that has made everything automated and changed the dynamics of every industry vertical.

How IoT took over SCADA and PLC?
PLC is the technology that was a companion to SCADA over the past few decades. But got outdated due to technological advancement.
Even PLCs receive data from sensors, which process that data and send it further as per the programmed parameters. PLCs can record and monitor real-time data such as operating temperature. It can automatically start and stop the processes and accordingly generate alarms if any malfunction is encountered.
However, the Industrial IoT (Internet of Things) made its existence in the market and evolved as a better technology compared to the traditional SCADA and PLC. Undoubtedly, its intelligent capabilities are highly adaptable to today’s modern industries. Most of the statistics from many industries concluded that strength of SCADA systems was relevant in Industry 4.0 revolution but where it got limited was to have a complete connected ecosystem so as to process it to rest of the business.
The Industrial IoT came up as a technology which got implemented on top of SCADA. Parameters like scalability, Data Analytics came into existence with the introduction of disruptive technology, IoT.
Data generated from SCADA systems still acts as a data source for the Industrial IoT. Industrial IoT focuses on analyzing the granular machine data so as to improve productivity whereas SCADA used to focus on monitoring and controlling. IoT has brought a wave of new business to change the landscape of SCADA.

How IoT differs from SCADA?
The following table illustrates how both differ:
S.NO |
![]() |
![]() |
![]() |
---|---|---|---|
1 | Scalability | In SCADA systems, due to the traditional architecture, when the number of users increases it degrades the performance drastically. Further, it also takes longer to run reports from plants that are in different countries and regions from the central plant. | IoT has the ability to ingest and process a huge amount of data from sensors and allows to connect anything of relevance using protocols like MQTT, HTTPS, XMPP, COAP, REST etc. which is powered by on-demand scalability due to serverless architecture. |
2 | Data Analytics | The main SCADA usage is for day-by-day plant operation and ingestion and storage of a finite amount of data without preservation of historical data for deeper analytics. | IoT involves long-term data retention to further analyze the data to predict maintenance schedules, reduce overall downtime, and extending equipment life. On top predictive analysis and preventive maintenance, capabilities are part of it which is supported by Machine Learning module. |
3 | Standardization | SCADA systems mostly use OPC for data gathering, it is a standard that has stood the test of time but its major disadvantage is that it relies on DCOM technology and devices cannot collect/exchange data with each other regardless of the footprint. | The primary goal of Industrial IoT is to standardize sensor networks, data gathering, and aggregation. IoT standards such as OPC UA are already being used to define real-time secure communication within a plant having different control devices and sensors from different vendors. Security is baked into IoT standards with support for MQTT, HTTPS, RAML etc. |
4 | Interoperability | In SCADA systems, devices not made by the same manufacturer cannot easily integrate. At times, even different versions from the same manufacturer present challenge in making them work interchangeably. Hence SCADA provides distributed business processes which work in siloes. | Industrial IoT ecosystems still remain fragmented but there are protocols such as MQTT which enable platforms to communicate across devices regardless of vendor. |
What future holds after a comparative analysis?
Conclusively, both SCADA and IoT involves sensors and data acquisition. They do differ in many aspects but share the common goal. SCADA is not a full control system whereas Industrial Internet of Things is made up of number of devices connected with each other. It allows objects to be controlled remotely across different network and architecture. But involving IoT with SCADA system provides a holistic understanding of the entire industrial premises in a more simplified way. In SCADA, where you have to manually generate analytics reports, with IoT-powered solution you can automate this process to save time and get quality output.
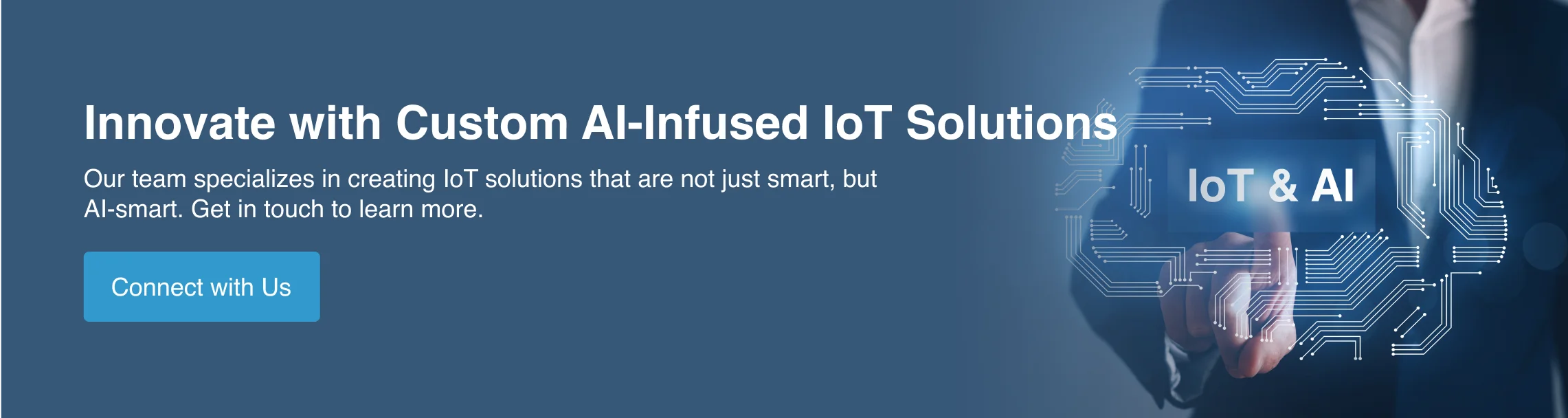